Additive Manufacturing
Additive manufacturing (AM) facilitates the fabrication of complex structures that would otherwise be difficult to make using other manufacturing methods. The spatial and dimensional errors that arise during fabrication using extrusion-based AM methods, like direct write (DW) printing, inhibit manufacturing parts with increased geometric fidelity. This research presents a method for measuring and correcting geometrical errors in DW-printed 3D periodic structures while they are fabricated. A process monitoring system is developed to measure the deposited material directly, and an iterative learning control (ILC) algorithm is implemented to compensate for the measured errors.
Process Monitoring
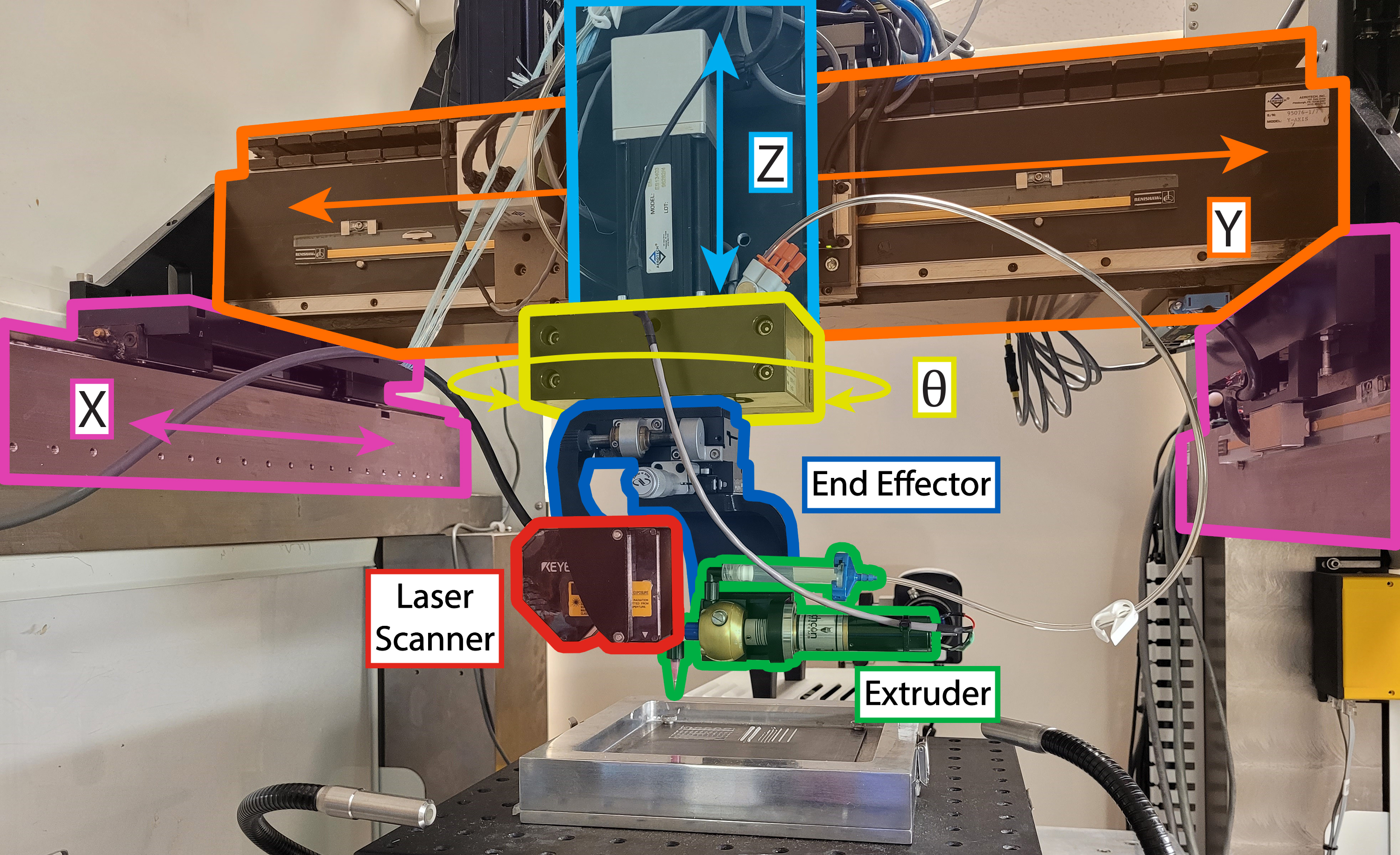
The DW printing system utilizes a 2D laser line scanner to take direct profile measurements of the deposited material. As the part is fabricated, the laser scanner follows a motion plan that tracks the print head’s position, generating time-delayed profile scans of the deposited material. An algorithm is developed to process the scans into a 2D projection of the structure and calculate the material’s bead width and centerline contour errors. This algorithm runs during the print, enabling the process monitoring system to determine the part’s geometric errors asynchronously, i.e., online but not in real time.
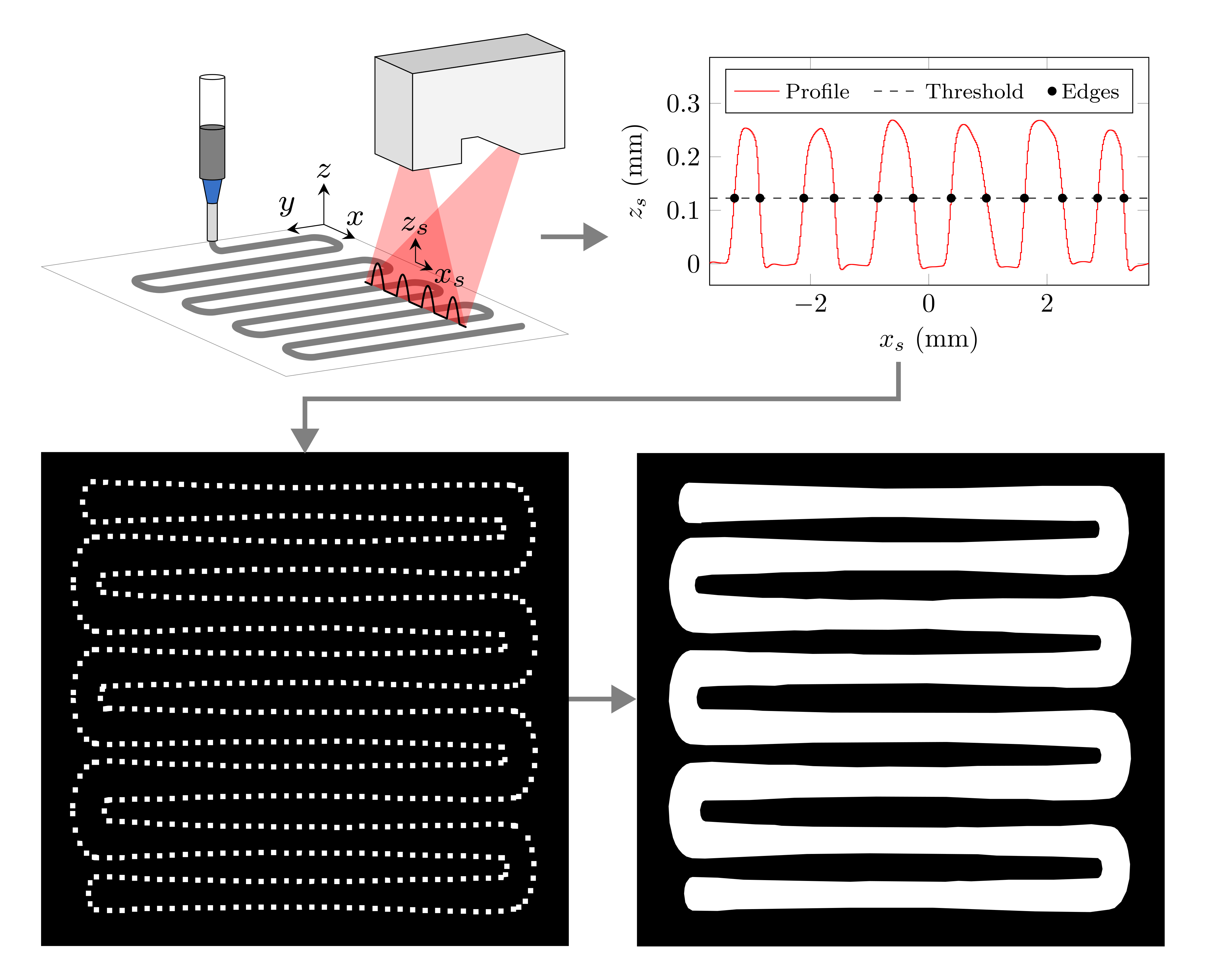
Control Strategy
Iterative learning control (ILC) is a feedforward control strategy implemented on systems that perform the same task multiple times. The premise behind ILC is that system performance can be improved by learning from previous task iterations. ILC exploits trajectory repetition to generate feedforward control signals by storing the control inputs and errors of past iterations and mapping them to the current iteration control inputs.
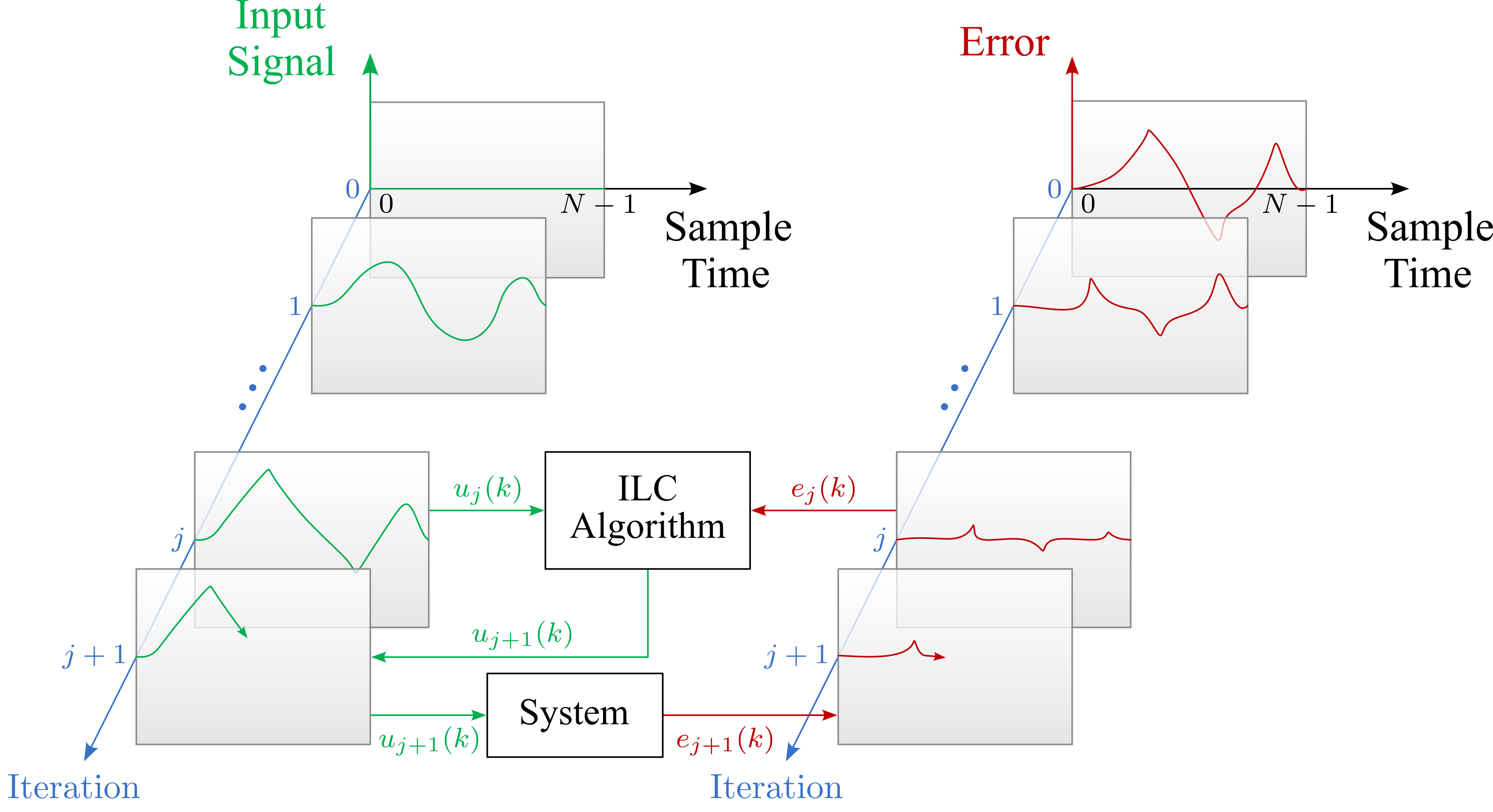
After each iteration, the previous input signal \(u_j(k)\) and the resulting error signal \(e_j(k)\) are used to calculate the updated input signal for the next iteration \(u_{j+1}(k)\).
ILC is well-suited for AM processes since they often include trajectory repetition—for example, repeating the same deposition trajectory between parts or layers. Here, the ILC algorithm learns the errors in the structure’s repetitive elements as they are printed using the online measurements, then modifies the inputs to the extrusion process to correct the errors in subsequently fabricated elements. With this implementation, the learning occurs concurrently with the printing process, which reduces the part’s errors as it prints.
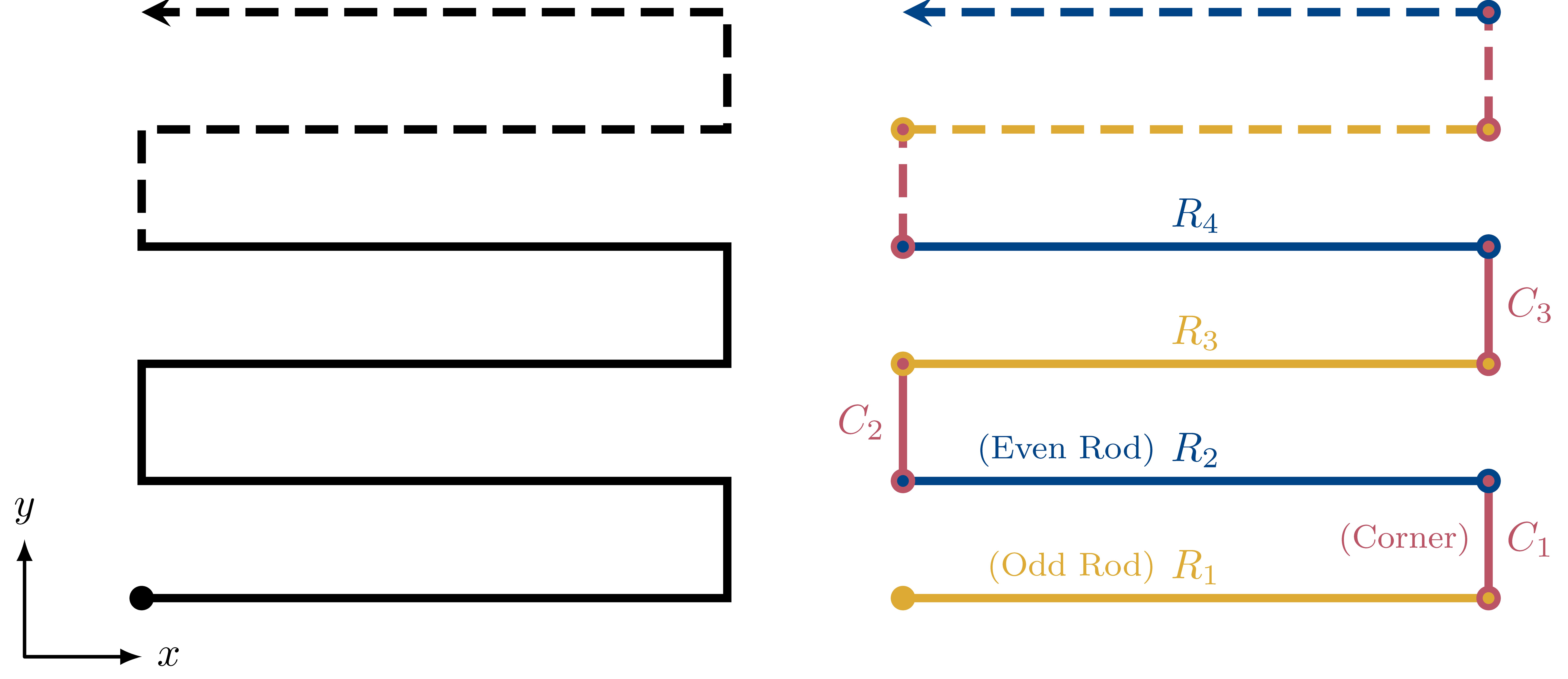
Experimental Validation
We experimentally validate the process monitoring and control strategy by fabricating 3D periodic lattice structures, specifically functionally graded scaffolds. The corrected prints utilizing the proposed process monitoring and control strategy show reduced errors in the material’s bead width.
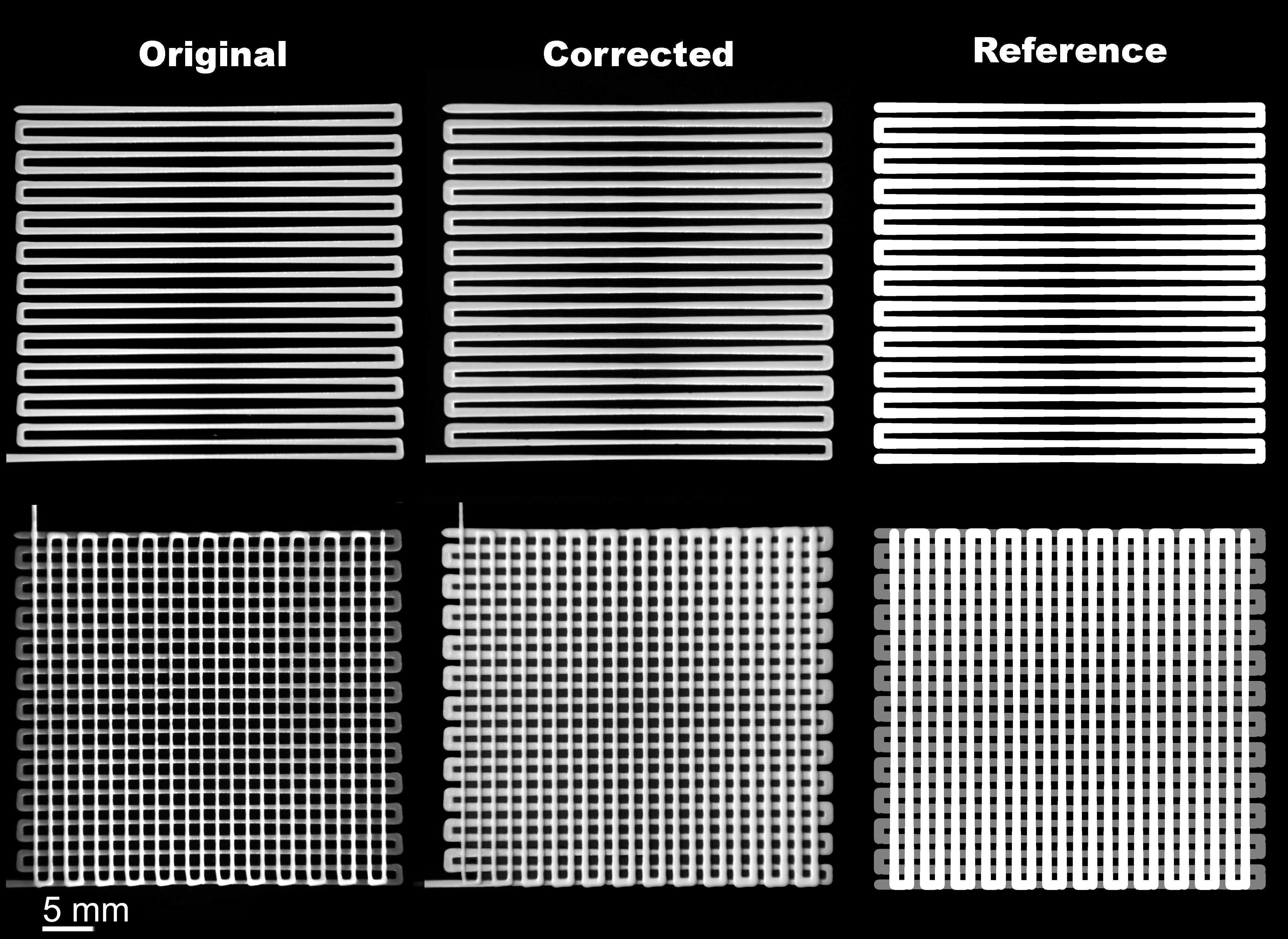
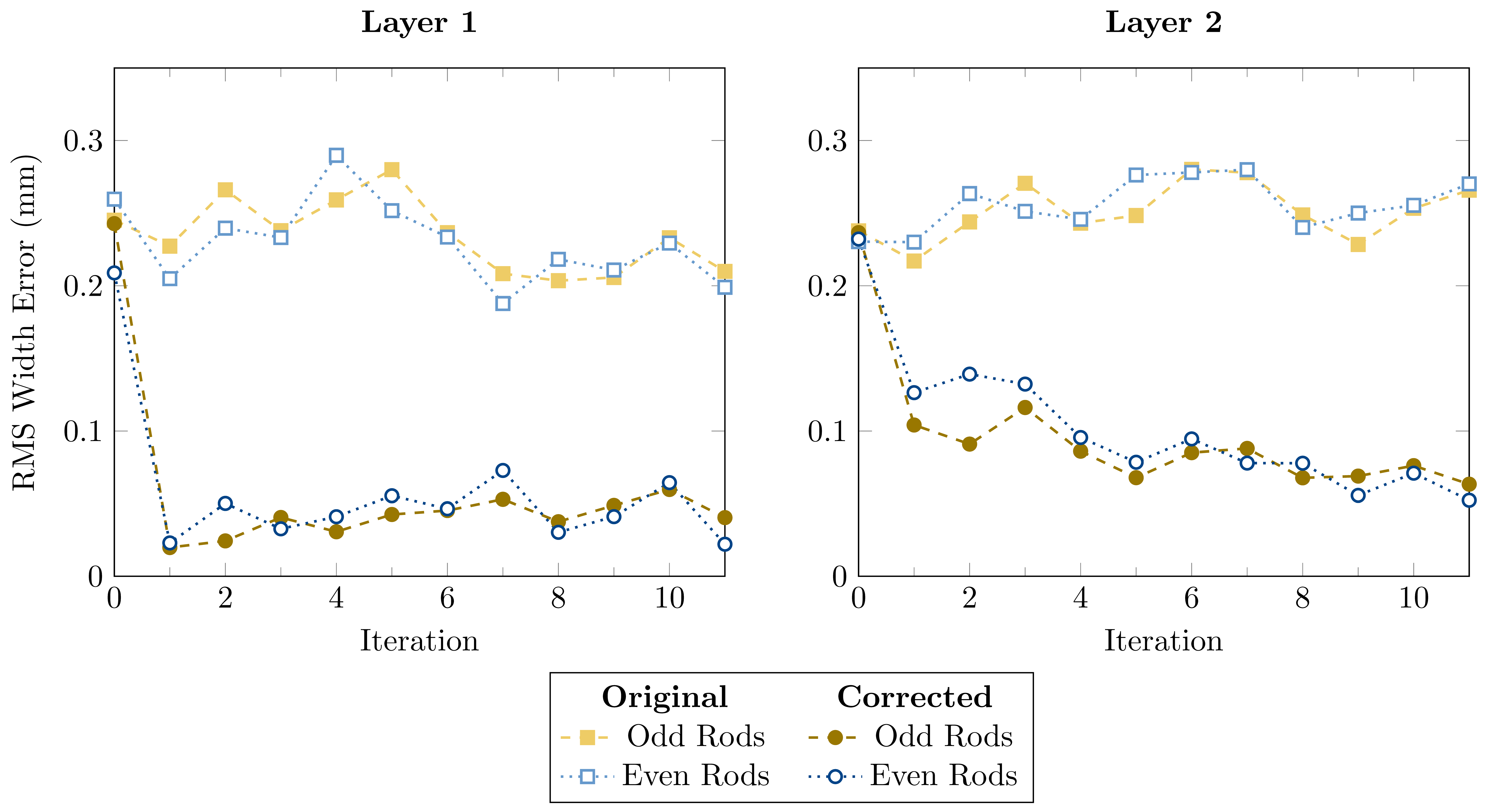